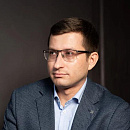
Проблема импортозамещения композитов для электротехнической продукции
11:10 / 18 декабря 2023
Наше предприятие ("Свердловский завод трансформаторов тока") в 2020 году перешагнуло 85-летний рубеж и является отечественным флагманом в вопросах проектирования и производства электротехнической продукции, трансформаторов различного назначения, а также иных устройств для отечественной энергетики. Среди прочего завод исторически был первопроходцем в области применения специального негорючего состава, применяемого в качестве основной изоляции, корпуса изделия. Данный состав пришел на замену трансформаторному маслу и со временем получил признание в эксплуатации, заняв достойное место на объектах отрасли, особенно в местах, требовательных к вопросам пожаробезопасности (электроэнергетика в широком смысле, объекты атомной отрасли, железнодорожный транспорт, объекты метро, жилые и промышленные здания и иные).
Составом, о котором далее пойдет речь является полимер – заливочный электроизоляционный компаунд. Данный материал является многокомпонентным и в зависимости от свойств может иметь различную природу основного связующего – эпоксидного, полиуретанового, кремнийооганического (силиконового) и циклоалифатического (для климатических исполнений УХЛ1). Данный компаунд состоит из нескольких компонентов, количество которых обычно от 2 до 5, в состав обязательно входят смола и отвердитель, а дальше уже в зависимости от свойств добавляется наполнитель, катализатор и пластификатор. От состава компонентов, соотношений и режимов отверждения могут сильно варьироваться свойства конечного отвержденного компаунда, а это значит, что для применения материалов в промышленных условиях, такие системы должны быть точно составлены и все их свойства должны быть обязательно испытаны в лабораторных условиях, а также проверены в эксплуатации.
Проблема же состоит в том, что в Российской Федерации отсутствует производственная база для изготовления данных материалов – отсутствуют производства базового сырья, не говоря уже о каких-то модификациях и базовых исследованиях, развития более специфических свойств, таких как, например, трудногорючесть, повышенная гидрофобность, и других. В России отсутствует производство эпоксидных смол даже базовых марок (а ведь в СССР согласно ГОСТу выпускали несколько марок эпоксидных смол), нет эпихлоргидрина для их производства, жидких отвердителей, отвердителей для полиуретанов, циклоалифатических смол, силиконовые электротехнические компаунды также не выпускаются, с катализаторами и пластификаторами тоже большие проблемы, даже по наполнителям есть вопросы, хотя к счастью базовый наполнитель все-таки российского производства.
Традиционные поставщики указанных выше компонентов – это известные в мире, и на российском рынке производители, в основном из стран США и Европы, которые с 2022 года закрыли свои поставки на рынок РФ после одного из принятых санкционных пакетов. Сегодня предприятия отрасли (и наше в том числе) переориентировались на поставщиков из Китая и Ирана, однако зависимость от валютных колебаний и длительные сроки поставок делают ситуацию далекой от разрешения.
Помимо производства химических составляющих, огромные силы и средства в других странах тратятся на исследования, например компания H. (ЕС) еще 10 лет назад могла под каждую задачу предложить 3-4 варианта заливочных электроизоляционных компаунда, а в каталоге насчитывалось около 3000 композиций под различные нужды, и данная компания при этом не охватывала всю область применения компаундов.
Также нужно понимать, что для замены компонентов компаунда, частично или полностью, требуется очень много исследований, изготовления нескольких серий образцов с последующими исследованиями на электрические и механические характеристики, проверка материала на различных конфигурациях изделий, повторные, верифицирующие испытания по множеству параметров. Замена компаунда занимает огромное количество средств и времени для предприятия, и также может быть отложенный эффект по качеству с течением времени, учитывая, что заявленный срок службы наших изделий составляет 30 лет, а реальный и до 50 лет.
Выходит, что критически важные для страны изделия имеют значимую зависимость от внешних обстоятельств, соответствующих компаний в РФ которые готовы заниматься новыми продуктами для электротехники практически нет. Главная причина, по которой их появление в ближайшей перспективе сомнительно, это тот факт, что в связи с отсутствием сырья экономически этот бизнес невозможен, пока не будет создана необходимая производственная база.
Сегодня на рынке РФ – порядка 10 крупных предприятий нашего профиля, и суммарный объем потребляемых импортных компонентов по самым скромным оценкам может составлять, как минимум, 500-1000 тонн в год. Также похожие связующие используются при изготовлении композиционных материалов, лакокрасочной продукции, клеев, наливных полов, и во многих других областях. Сегодня они в подавляющем большинстве – импортного производства.
Рассчитываю, что государственные структуры, совместно с крупным частным капиталом, обратят внимание на озвученную проблему и примут своевременные меры по развитию данного направления, потому что восстановление этой отрасли потребует колоссальных усилий и вложений, включающих в себя сложные и в техническом, и в экономическом, и в экологическом плане производства, научную базу, исследования с высокими затратами на оборудование, а также человеческие ресурсы.
Однако кумулятивный эффект от реализации этого плана поможет совершить качественный рывок во многих отраслях, не только электротехнике. Повысить внутреннюю кооперацию, сделать еще один серьезный шаг по направлению к технологическому суверенитету.
Автор: Максим Суетин, технический директор "Свердловского завода трансформаторов тока"
RUPEC в Telegram
0 комментариев